How to Create an Effective Maintenance Log Book Sample for Excel
How to Create an Effective Maintenance Log Book Sample for Excel - There are a lot of affordable templates out there, but it can be easy to feel like a lot of the best cost a amount of money, require best special design template. Making the best template format choice is way to your template success. And if at this time you are looking for information and ideas regarding the How to Create an Effective Maintenance Log Book Sample for Excel then, you are in the perfect place. Get this How to Create an Effective Maintenance Log Book Sample for Excel for free here. We hope this post How to Create an Effective Maintenance Log Book Sample for Excel inspired you and help you what you are looking for.
The maintenance log book sample is a tool that helps keep track of maintenance activities and is a valuable asset for any organization that wants to ensure optimal performance and longevity of their equipment. For instance, an oil and gas company might use a maintenance log book sample to record details of maintenance performed on their pipelines, including the date, time, and type of work completed, as well as the name of the technician who performed the work.
The maintenance log book sample has become increasingly important in recent years as organizations have come to realize the benefits of preventive maintenance. By keeping a detailed record of maintenance activities, organizations can identify potential problems before they become major issues, which can save time and money in the long run. Additionally, the maintenance log book sample can be used to track warranty information and to identify trends in maintenance needs, which can help organizations to improve their maintenance practices.
The use of maintenance log book samples has a long history, dating back to the early days of the Industrial Revolution. In the 18th century, mill owners began using maintenance log books to track the performance of their machinery. This allowed them to identify problems early on and to make repairs before they caused major disruptions to production. Today, maintenance log book samples are used in a wide variety of industries, from manufacturing to healthcare.
Maintenance Log Book Sample
A maintenance log book sample is a crucial tool for organizations to ensure optimal performance and longevity of their equipment. It helps keep track of maintenance activities, providing valuable insights into various aspects that affect maintenance practices. Key aspects to consider include:
- Equipment details
- Maintenance schedule
- Maintenance tasks
- Spare parts inventory
- Technician assignments
- Maintenance costs
- Warranty information
- Maintenance history
- Compliance records
These aspects are interconnected and play a vital role in effective maintenance management. Equipment details provide a comprehensive understanding of the assets being maintained, while the maintenance schedule ensures timely servicing. Maintenance tasks outline the specific actions required to maintain the equipment, and spare parts inventory helps prevent downtime by ensuring availability of necessary components. Technician assignments optimize resource allocation, and maintenance costs provide insights into budgetary requirements. Warranty information ensures coverage for repairs, and maintenance history offers a chronological record of all maintenance activities. Compliance records demonstrate adherence to industry standards, and maintenance log book samples serve as a valuable tool for audits and inspections.
Equipment details
Equipment details are a critical component of any maintenance log book sample, as they provide essential information about the equipment being maintained. This information can include the equipment’s make, model, serial number, location, and maintenance history. By having this information readily available, maintenance technicians can quickly and easily identify the equipment that needs to be serviced, as well as the specific maintenance tasks that need to be performed. For example, if a maintenance technician is called to service a piece of equipment, they can use the maintenance log book sample to look up the equipment’s serial number and maintenance history. This information can help the technician to identify the root cause of the problem and to determine the best course of action.
In addition to providing essential information about the equipment being maintained, equipment details can also be used to track the performance of the equipment over time. By recording the dates and times that maintenance tasks are performed, as well as the specific tasks that are performed, maintenance managers can identify trends in equipment performance. This information can be used to improve maintenance practices and to prevent future problems.
Overall, equipment details are a critical component of any maintenance log book sample. By providing essential information about the equipment being maintained, as well as tracking the performance of the equipment over time, equipment details can help maintenance managers to improve maintenance practices and to prevent future problems.
Maintenance schedule
A maintenance schedule is an essential part of any maintenance log book sample, as it provides a roadmap for the maintenance activities that need to be performed on a piece of equipment. A well-defined maintenance schedule can help to prevent equipment failures, reduce downtime, and extend the life of the equipment.
-
Maintenance frequency
The maintenance frequency is the interval at which maintenance tasks are performed. The frequency of maintenance will vary depending on the type of equipment, the operating environment, and the manufacturer’s recommendations. -
Maintenance tasks
The maintenance tasks are the specific actions that need to be performed during maintenance. The tasks will vary depending on the type of equipment, but may include things like inspections, cleaning, lubrication, and repairs. -
Maintenance procedures
The maintenance procedures are the step-by-step instructions for performing maintenance tasks. The procedures should be clear and concise, and should be followed by all maintenance personnel. -
Maintenance records
The maintenance records are a record of all maintenance activities that have been performed on a piece of equipment. The records should include the date and time of the maintenance, the tasks that were performed, and the name of the person who performed the maintenance.
By following a well-defined maintenance schedule, organizations can help to ensure that their equipment is properly maintained and operating at peak efficiency. This can help to prevent equipment failures, reduce downtime, and extend the life of the equipment.
Maintenance tasks
Maintenance tasks are a critical component of any maintenance log book sample, as they provide a detailed record of the work that has been performed on a piece of equipment. This information can be used to track the performance of the equipment over time, identify trends, and plan for future maintenance.
The specific maintenance tasks that are performed will vary depending on the type of equipment, but may include things like inspections, cleaning, lubrication, and repairs. It is important to develop a maintenance schedule that outlines the frequency and type of maintenance tasks that should be performed on each piece of equipment. This schedule should be based on the manufacturer’s recommendations, as well as the operating environment and the equipment’s history.
By completing maintenance tasks on a regular basis, organizations can help to prevent equipment failures, reduce downtime, and extend the life of their equipment. This can save money in the long run and help to ensure that the equipment is operating at peak efficiency.
For example, a manufacturing company might use a maintenance log book sample to track the maintenance tasks that are performed on their production equipment. This information can be used to identify trends in equipment performance, such as increased downtime or maintenance costs. This information can then be used to improve maintenance practices and prevent future problems.
Maintenance tasks are an essential part of any maintenance program. By completing maintenance tasks on a regular basis, organizations can help to ensure that their equipment is operating at peak efficiency and that they are getting the most out of their investment.
Spare parts inventory
Spare parts inventory is a critical component of any maintenance log book sample, as it helps to ensure that the necessary parts are available to perform maintenance tasks quickly and efficiently. Without a well-stocked spare parts inventory, maintenance technicians may have to wait for parts to be ordered and delivered, which can lead to downtime and lost productivity.
The size and composition of a spare parts inventory will vary depending on the type of equipment being maintained and the operating environment. However, there are some general guidelines that can be followed to ensure that an adequate supply of spare parts is available. First, it is important to identify the critical spare parts that are essential for keeping the equipment running. These parts should be stocked in sufficient quantities to meet the expected demand. Second, it is important to consider the lead time for ordering and delivering spare parts. Parts that have a long lead time should be stocked in larger quantities to avoid stockouts.
Real-life examples of spare parts inventory management can be found in a variety of industries. For instance, an airline might maintain a spare parts inventory for its fleet of aircraft. This inventory would include critical parts such as engines, landing gear, andavionics. By having these parts on hand, the airline can quickly and efficiently repair its aircraft and minimize downtime. Another example of spare parts inventory management can be found in the manufacturing industry. A manufacturing plant might maintain a spare parts inventory for its production equipment. This inventory would include critical parts such as bearings, gears, and motors. By having these parts on hand, the manufacturing plant can quickly and efficiently repair its equipment and minimize downtime.
The practical applications of understanding the connection between spare parts inventory and maintenance log book sample are numerous. For instance, this understanding can help organizations to improve their maintenance practices and reduce downtime. By ensuring that the necessary spare parts are available, organizations can quickly and efficiently repair their equipment and get it back up and running. This can help to reduce downtime and lost productivity. Additionally, this understanding can help organizations to save money on maintenance costs. By stocking the right spare parts in the right quantities, organizations can avoid the need to order and deliver parts on an emergency basis, which can be expensive.
Technician assignments
Technician assignments are an integral part of the maintenance log book sample, serving as a critical bridge between maintenance tasks and their execution by qualified personnel. By assigning specific tasks to qualified technicians, organizations can ensure that maintenance is performed efficiently, effectively, and in accordance with established standards. The various facets of technician assignments contribute to the overall effectiveness of the maintenance log book sample.
-
Skill matching
Matching the skills and expertise of technicians to specific maintenance tasks is crucial for ensuring that tasks are performed correctly and efficiently. A maintenance log book sample should consider the skill sets of available technicians and assign tasks accordingly. -
Workforce optimization
Effective technician assignments optimize the utilization of workforce resources. By assigning tasks based on technician availability, workload, and skillset, organizations can ensure that all technicians are fully utilized and that maintenance tasks are completed on time. -
Accountability
Clear technician assignments establish accountability for the completion of maintenance tasks. By assigning specific tasks to named individuals, organizations can track the progress of maintenance activities and hold technicians responsible for the quality of their work. -
Safety
Assigning tasks to qualified technicians helps to ensure the safety of both the technicians and the equipment being maintained. By matching tasks to technicians with the appropriate training and experience, organizations can minimize the risk of accidents or injuries during maintenance activities.
In summary, technician assignments are a critical component of the maintenance log book sample, ensuring that maintenance tasks are executed efficiently, effectively, and safely. By considering the skill sets, availability, and workload of technicians, organizations can optimize their workforce and ensure that maintenance tasks are completed to a high standard.
Maintenance costs
Maintenance costs are a significant aspect of the maintenance log book sample, providing insights into the financial implications of maintaining equipment and assets. This information is crucial for organizations to plan and allocate resources effectively, ensuring optimal equipment performance and minimizing downtime.
-
Labor costs
Labor costs encompass the wages and benefits paid to technicians and engineers responsible for performing maintenance tasks. These costs can vary based on factors such as skill level, experience, and industry rates. -
Parts and materials costs
Parts and materials costs include the expenses associated with purchasing or replacing components, spare parts, and consumables used during maintenance activities. This can range from small items like gaskets and filters to major components like engines or circuit boards. -
Equipment costs
Equipment costs refer to the expenses incurred for purchasing, leasing, or renting specialized tools, machinery, or equipment necessary for performing maintenance tasks. These costs can be significant, especially for complex or heavy-duty equipment. -
Downtime costs
Downtime costs represent the financial losses incurred when equipment is unavailable due to maintenance or repairs. This can include lost production, delayed shipments, or penalties for missed deadlines. Downtime costs can be substantial, particularly for critical equipment or processes.
Understanding maintenance costs is essential for organizations to prioritize and optimize maintenance activities. By tracking and analyzing these costs, organizations can identify areas for improvement, reduce unnecessary expenses, and make informed decisions regarding equipment maintenance and replacement strategies. A well-maintained maintenance log book sample provides a valuable foundation for effective cost management and proactive maintenance planning.
Warranty information
Warranty information plays a crucial role in the maintenance and upkeep of equipment and assets, providing valuable insights for organizations to make informed decisions regarding maintenance strategies and resource allocation. A comprehensive maintenance log book sample should include detailed warranty information to ensure optimal equipment performance and minimize downtime.
-
Coverage details
Warranty coverage details outline the specific components, parts, and labor covered under the warranty agreement. This information helps organizations understand the extent of their coverage and the potential costs associated with repairs or replacements.
-
Warranty period
The warranty period defines the duration of time during which the manufacturer or service provider guarantees the equipment’s performance and functionality. Understanding the warranty period allows organizations to plan maintenance activities and schedule repairs or replacements accordingly.
-
Warranty exclusions
Warranty exclusions specify the conditions or circumstances under which the warranty coverage does not apply. This information helps organizations identify any limitations or exceptions to the warranty and plan for potential expenses outside the scope of coverage.
-
Warranty claims process
The warranty claims process outlines the steps and procedures for filing and processing warranty claims. This information ensures that organizations can effectively communicate with the manufacturer or service provider and obtain necessary repairs or replacements in a timely manner.
Warranty information is essential for organizations to optimize maintenance practices and minimize equipment downtime. By understanding the coverage details, warranty period, exclusions, and claims process, organizations can proactively plan maintenance activities, allocate resources effectively, and make informed decisions regarding equipment maintenance and replacement strategies.
Maintenance history
Maintenance history is an indispensable component of a maintenance log book sample, providing a comprehensive record of past maintenance activities, repairs, and inspections performed on a particular piece of equipment or asset. This information is invaluable for organizations to understand the equipment’s performance over time, identify potential issues, and plan for future maintenance needs.
-
Repair records
Repair records document instances of equipment breakdowns, the nature of the repairs performed, and the parts or components that were replaced. This information helps organizations identify recurring problems and assess the effectiveness of previous repairs. -
Inspection reports
Inspection reports provide detailed accounts of regular or scheduled inspections, including observations, measurements, and any identified defects or areas of concern. These reports help organizations monitor equipment condition and plan for preventive maintenance. -
Maintenance schedules
Maintenance schedules outline the planned maintenance activities for a specific piece of equipment, including the frequency and type of maintenance tasks to be performed. This information ensures that maintenance is performed proactively and in accordance with manufacturer recommendations. -
Parts inventory
Parts inventory records track the availability and usage of spare parts and components for the equipment. This information helps organizations maintain optimal inventory levels and avoid unnecessary downtime due to lack of parts.
Collectively, these facets of maintenance history provide organizations with a valuable resource for optimizing maintenance practices, reducing equipment downtime, and extending the lifespan of their assets. By leveraging maintenance history data, organizations can make informed decisions about maintenance strategies, resource allocation, and equipment replacement.
Compliance records
Maintenance log book samples that include compliance records provide organizations with a valuable tool for ensuring regulatory compliance and minimizing legal risks. Compliance records document the actions taken to maintain equipment and assets in accordance with established standards, regulations, and industry best practices. These records serve as evidence of an organization’s commitment to safety, environmental protection, and quality control.
By maintaining accurate and up-to-date compliance records, organizations can demonstrate their adherence to regulatory requirements and industry standards. This can help to avoid fines, penalties, and legal liabilities. Compliance records also provide a basis for internal audits and quality control measures, helping organizations to identify areas for improvement and ensure continuous compliance.
Real-life examples of compliance records within maintenance log book samples include:
- Records of inspections and tests performed to ensure compliance with safety regulations
- Documentation of maintenance activities and repairs carried out in accordance with manufacturer specifications
- Records of training and certification for technicians and engineers responsible for maintenance tasks
- Environmental monitoring data and reports to demonstrate compliance with environmental regulations
The practical applications of understanding the connection between compliance records and maintenance log book samples are numerous. Organizations can use this understanding to:
- Improve their compliance posture and reduce legal risks
- Enhance the accuracy and reliability of their maintenance records
- Facilitate internal audits and quality control measures
- Enhance their reputation as a responsible and compliant organization
In summary, compliance records are a critical component of maintenance log book samples, providing organizations with a valuable tool for ensuring regulatory compliance, minimizing legal risks, and improving maintenance practices. By maintaining accurate and up-to-date compliance records, organizations can demonstrate their commitment to safety, environmental protection, and quality control, while also enhancing their reputation and competitiveness in the marketplace.
FAQs on Maintenance Log Book Sample
This section addresses frequently asked questions about Maintenance Log Book Sample, providing answers to common queries and clarifying important aspects.
Question 1: What is the purpose of a Maintenance Log Book Sample?
A Maintenance Log Book Sample serves as a comprehensive record of maintenance activities performed on equipment and assets, providing valuable insights for organizations to optimize their maintenance practices.
Question 2: What are the key components of a Maintenance Log Book Sample?
Key components include equipment details, maintenance schedule, maintenance tasks, spare parts inventory, technician assignments, maintenance costs, warranty information, maintenance history, and compliance records.
Question 3: How does a Maintenance Log Book Sample help organizations?
It assists organizations in tracking maintenance activities, optimizing resource allocation, predicting maintenance needs, ensuring regulatory compliance, and improving overall equipment performance and longevity.
Question 4: Who should use a Maintenance Log Book Sample?
Organizations across various industries, including manufacturing, transportation, healthcare, and facility management, can benefit from using a Maintenance Log Book Sample.
Question 5: What are the benefits of using a Maintenance Log Book Sample?
Benefits include improved maintenance efficiency, reduced downtime, extended equipment lifespan, enhanced safety, and increased regulatory compliance.
Question 6: How do I create a Maintenance Log Book Sample?
Organizations can develop a Maintenance Log Book Sample tailored to their specific equipment and maintenance needs by considering the key components and industry best practices.
Question 7: What is the importance of maintaining accurate Maintenance Log Book Samples?
Accurate records ensure reliable data for analysis, decision-making, and compliance purposes, helping organizations improve their maintenance strategies and overall equipment management.
These FAQs provide essential insights into Maintenance Log Book Samples, highlighting their significance and the key considerations for effective implementation. By leveraging this information, organizations can enhance their maintenance practices, optimize resource allocation, and ultimately achieve improved equipment performance and reliability.
The next section of this article delves into the practical applications of Maintenance Log Book Samples, showcasing real-life examples and industry use cases to further illustrate their value and impact.
Tips for Maintaining Accurate Maintenance Log Book Samples
Maintaining accurate and comprehensive Maintenance Log Book Samples is essential for effective equipment management and regulatory compliance. Here are a few detailed tips to assist organizations in achieving this goal:
Tip 1: Establish a Clear Maintenance Schedule
Develop a structured maintenance schedule outlining the frequency and type of maintenance tasks for each piece of equipment, ensuring regular upkeep and timely interventions.
Tip 2: Use Digital Maintenance Log Book Software
Consider implementing digital maintenance log book software to streamline record-keeping, improve data accuracy, and facilitate real-time updates from the field.
Tip 3: Train Maintenance Personnel
Provide thorough training to maintenance personnel on the importance of accurate record-keeping, ensuring they understand the purpose and significance of detailed maintenance logs.
Tip 4: Encourage Accurate and Timely Reporting
Establish a culture of accurate and timely reporting by emphasizing the consequences of inaccurate or delayed maintenance records, highlighting their impact on equipment performance, safety, and compliance.
Tip 5: Implement a System for Regular Review and Updates
Assign responsibility for regularly reviewing and updating maintenance log book samples to ensure accuracy, completeness, and alignment with maintenance activities performed.
Tip 6: Use Clear and Consistent Terminology
Establish and adhere to clear and consistent terminology when recording maintenance activities, ensuring accurate communication and avoiding misunderstandings among maintenance personnel.
Tip 7: Include All Relevant Details
Ensure that maintenance log book samples capture all relevant details, including the date, time, technician name, maintenance tasks performed, parts replaced, and any observations or recommendations.
Tip 8: Secure Maintenance Log Book Samples
Implement measures to secure maintenance log book samples from unauthorized access or tampering, ensuring the integrity and confidentiality of maintenance records.
Tip 9: Regularly Audit Maintenance Log Book Samples
Conduct regular audits of maintenance log book samples to assess accuracy, completeness, and compliance with established procedures, identifying areas for improvement.
Tip 10: Leverage Maintenance Log Book Samples for Continuous Improvement
Analyze maintenance log book samples to identify trends, patterns, and areas for improvement in maintenance practices, optimizing maintenance strategies and enhancing equipment performance.
By following these tips, organizations can significantly improve the accuracy and completeness of their Maintenance Log Book Samples, leading to enhanced equipment management, reduced downtime, and improved compliance. This lays the foundation for the concluding section of this article, which will discuss the long-term benefits and strategic implications of maintaining accurate maintenance records.
Conclusion
In conclusion, Maintenance Log Book Samples serve as indispensable tools for organizations to achieve optimal maintenance practices and ensure the longevity of their equipment. This article has explored the multifaceted aspects of Maintenance Log Book Samples, highlighting their significance in various industries and their impact on equipment performance, regulatory compliance, and cost optimization.
Key insights from this article include the importance of establishing a comprehensive maintenance schedule, involving maintenance personnel in the maintenance process, and leveraging digital tools to enhance efficiency and accuracy. By maintaining accurate and up-to-date Maintenance Log Book Samples, organizations can proactively address maintenance needs, minimize downtime, and maximize the return on their equipment investments.
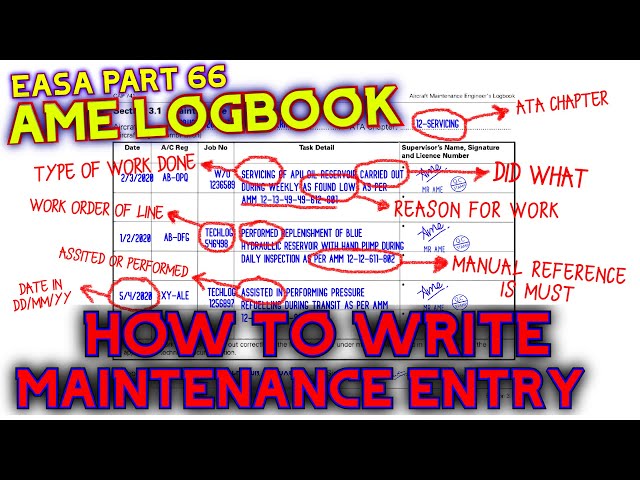
How to Create an Effective Maintenance Log Book Sample for Excel was posted in April 8, 2024 at 3:51 am. If you wanna have it as yours, please click the Pictures and you will go to click right mouse then Save Image As and Click Save and download the How to Create an Effective Maintenance Log Book Sample for Excel Picture.. Don’t forget to share this picture with others via Facebook, Twitter, Pinterest or other social medias! we do hope you'll get inspired by ExcelKayra... Thanks again! If you have any DMCA issues on this post, please contact us!